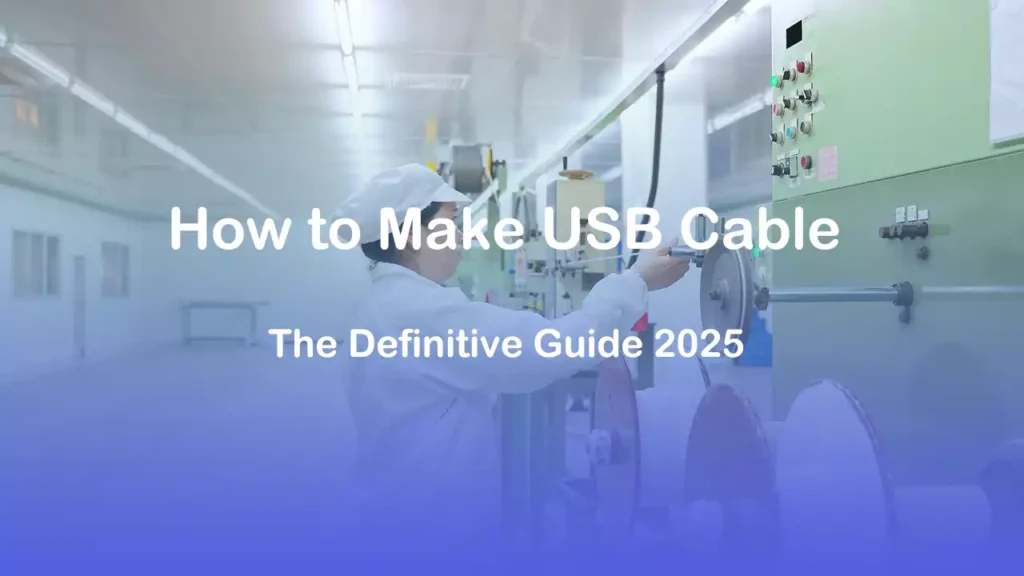
Table of Contents
USB cables are the unsung heroes of our connected world, powering everything from smartphones to industrial devices. But not all cables are created equal, the bad materials or flawed manufacturing can lead to slow charging, data corruption, or even safety hazards.
As a USB-IF certified manufacturer with 24+ years of expertise, Cablink combines precision engineering with rigorous quality control to deliver cables that meet global standards. In this guide, we’ll demystify the USB cable manufacturing process, explain why certification matters, and showcase how Cablink ensures unmatched reliability for consumers and businesses.
Introduction
The average household owns over 10 USB cables, yet fewer than 30% of users prioritize certified, high-quality options. This oversight risks device damage, inefficient charging, and security vulnerabilities. For manufacturers, producing reliable USB cables requires more than just assembling wires – it demands adherence to strict material standards, advanced engineering, and compliance with protocols set by the USB Implementers Forum (USB-IF).
At Cablink, we specialize in crafting USB cables that exceed industry benchmarks. Our products, ranging from USB-C to Lightning cables to 40Gbps USB4 solutions, are trusted by tech giants and consumers alike. This guide will walk you through the science of USB cable production and explain how Cablink’s commitment to excellence sets us apart.
Essential Materials for USB Cable Manufacturing
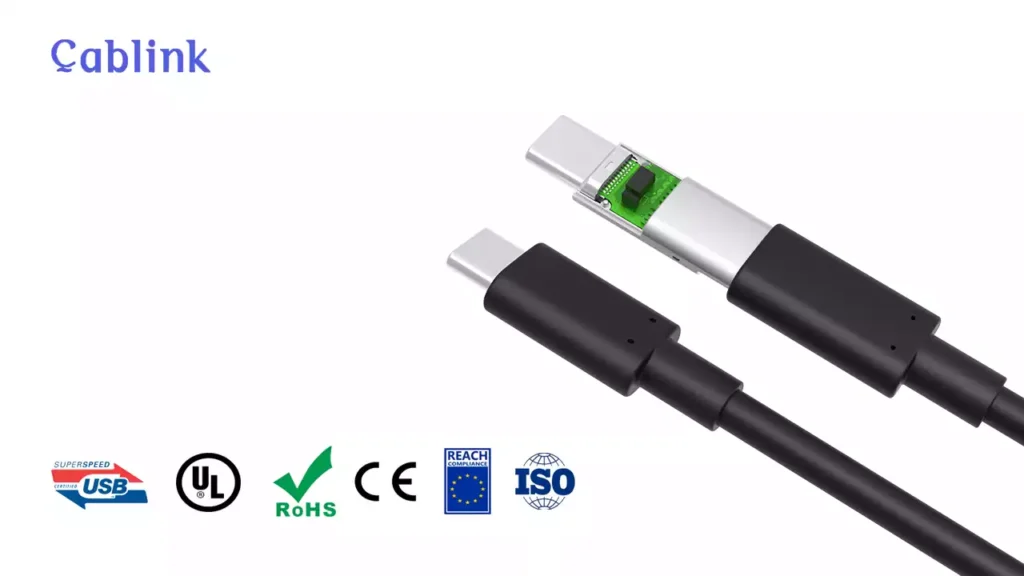
Conductors: The Lifeline of Data and Power
- Oxygen-Free Copper (OFC):
OFC’s 99.95% purity minimizes electrical resistance, ensuring efficient power delivery and high-speed data transfer (e.g., USB4’s 40Gbps capability). Cheap alternatives like copper-clad aluminum (CCA) degrade over time, causing voltage drops. - Tinning:
A micro-thin tin coating protects copper strands from oxidation, especially in humid environments.
Insulation: Balancing Flexibility and Safety
- PVC vs. TPE:
While PVC is cost-effective, Cablink uses thermoplastic elastomer (TPE) for premium cables. TPE resists temperatures from -40°C to 130°C (-40℉ to 266℉)and contains no harmful phthalates.
Shielding: Defending Against Interference
- Dual-Layer Shielding:
A foil layer blocks static interference, while braided shielding (95% coverage density) neutralizes electromagnetic waves. Critical for USB 3.2/4.0 cables carrying 100W power.
Outer Jacket: Durability Meets Design
- Nylon-Reinforced Jacketing:
Our cables undergo 10,000+ bend tests (USB-IF requirement: 5,000 cycles). The textured finish improves grip and resists tangling.
Connectors: Precision Meets Compatibility
- Gold-Plated Contacts:
With 50μ” gold plating of the connectors (vs. standard 15μ”), Cablink’s USB-C and USB-A connectors reduce insertion wear and maintain stable conductivity.
USB-IF Certification: Non-Negotiable Compliance
- Certified E-Marker Chips:
Embedded chips validate power delivery (PD 3.1), data protocols, and cable capabilities. Non-compliant cables risk damaging devices like MacBooks or gaming consoles.
Step-by-Step Manufacturing Process
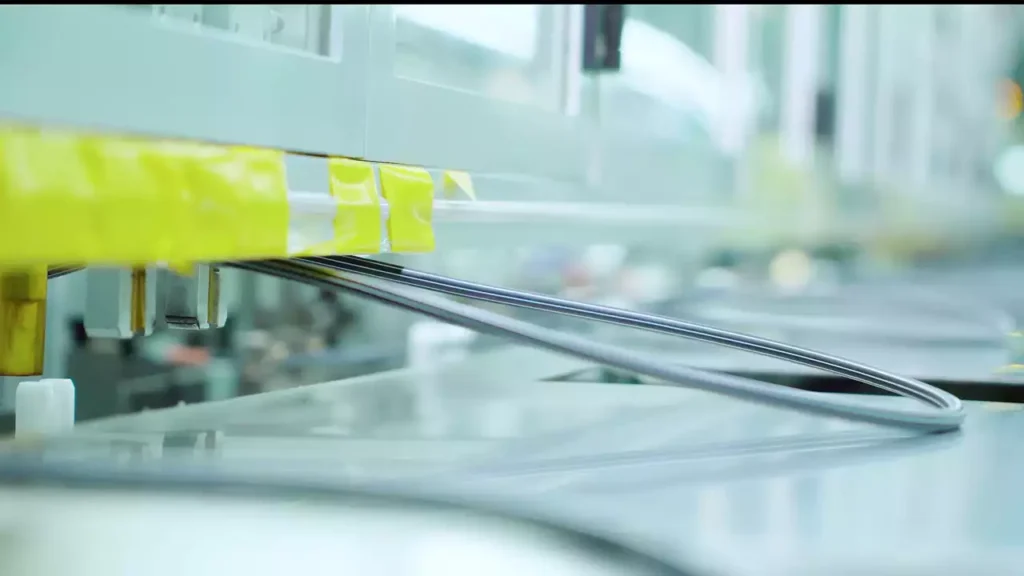
Wire Preparation
Stranding:
32 AWG copper strands are twisted into bundles, optimizing flexibility without sacrificing conductivity.
In factories, the Stranding process is usually operated by machines to ensure the stability of quality. Therefore, this process is generally not used much in DIY, mainly because it is difficult to control the quality. Poor winding will not only affect the appearance, but also cause unstable power or signal transmission, and even uncontrollable risks. Therefore, it is recommended that DIY players buy finished copper wires.
Insulation Extrusion
TPE is applied via laser-measured extruders, ensuring uniform thickness (±0.02mm tolerance).
In fact, not only TPE materials, but also PVC materials are widely used in USB cables. The biggest advantage of PVC is that it is relatively cheap and has very good performance.
PVC has good electrical insulation, is easy to extrude and flame retardant, and can be recycled. Its temperature range can reach -15℃ to +105℃ (5℉ to 221℉).
Shielding & Pairing
Foiling
Aluminum-Mylar foil is wrapped around conductors, followed by spiral-braided shielding for 360° protection.
The shielding layer is very important for USB cables, and can be said to be the backbone of USB cables. In daily use, we will inevitably encounter bending or stretching. At this time, the shielding layer can not only reduce the lateral or longitudinal force, effectively protect the copper wire, but also reduce electromagnetic interference.
Twisting
High-speed data pairs (e.g., SuperSpeed+ in USB4) are twisted at precise angles to cancel crosstalk. The purpose of this step is to lay out the power line and signal line in layers to reduce the interference of current transmission on signal transmission, which is very important in high-speed USB cables (eg. USB 4.0 cable).
In the actual production process, it is still necessary to rely on professional production equipment for precise control to ensure that the two types of cables are fully isolated, otherwise it will affect performance and even cause safety problems.
Assembly
Automated Soldering:
Robotic arms solder wires to connector pins with 0.1mm precision, eliminating human error.
The solder joints between the wire and the connector are also very important. This step is still very popular in USB cable DIY, because as time goes by, welding will inevitably have cold solder joints or poor solder joints. The advantage of using a robotic arm for welding is that the accuracy is controllable, and the robotic arm welding generally has full solder joints and evenly distributed solder, which can minimize the probability of problems.
Overmolding
Overmolding refers to the process of secondary injection molding and sealing the USB cable and connector. It not only increases the aesthetics of the cable, but most importantly, it can better protect the connector after one-piece molding and significantly increase the life of the connector. As we all know, electrical products are very sensitive to water and dust.
Tips: Connector heads are molded with strain relief collars, rated to withstand 50N of pull force.
Testing & Certification
Electrical Test
This test mainly tests whether the voltage and current values of each pin meet the standard definition. Especially after the subsequent USB Type C interface adds power supply characteristics, the USB cable will transmit current, so the stability of electrical performance is crucial.
Connection Tests
This test mainly tests the function and power supply of each pin of the connector, as well as the data that deviates from the tolerance range. For factories, the data of these tests can often be collected and tested by one device.
Cable Tests
The purpose of this test is to check CPUT applies Ra, discharges Vconn, and is capable of communicating at its highest USB speed.
This part of the test actually includes Alternate Mode Test and the standard definition of CPUT voltages for USB 3.2 and USB 4, as well as detailed requirements for the speeds that need to be achieved within the voltage range, so that the USB cable can be guaranteed to fully meet the standards set by USB-IF when it reaches the hands of consumers.
Of course, there are also common bending tests, durability tests and other conventional tests, which can actually be included in the cable test, because we have already discussed them in detail before, so I will not repeat them here.
Why USB-IF Certification Cannot Be Compromised
Uncertified cables often fail to “handshake” properly with devices, leading to:
- Overheating: Poorly regulated PD can overstress batteries.
- Data Loss: Incorrect impedance causes packet errors.
- Voided Warranties: Brands like Apple deny support for uncertified accessories.
Cablink’s certification ensures:
- Universal Compatibility: Works flawlessly with Samsung DeX, PlayStation VR2, and other advanced systems.
- Future-Proofing: Supports emerging standards like USB4 2.0’s 80Gbps mode.
Cablink’s USB-IF Certified Cables

As a professional USB cable manufacturer, we provide the following services:
What We Offers
Cablink provides customized USB cable services, covering cables from USB 2.0 to the latest USB 4.0 versions.
Not only that, we also provide OEM services for HDMI cables and peripheral products.
Why Cablink?
With 24 years of industry experience, the factory has automated production equipment, 1500+ skilled workers, and dozens of industry certificates, including UL, ETL, DELTA, HDMI, VESA, USB-IF, MMFI, RoHS, and REACH certifications, and more than 2000+ cooperative customers.
Conclusion
Building a USB cable isn’t just about connecting wires – it’s about engineering a product that survives daily abuse while delivering peak performance. Cablink’s relentless focus on material quality, USB-IF compliance, and real-world testing ensures our cables outperform competitors.
Whether you’re a gamer needing lag-free VR headsets or an IT manager deploying IoT sensors, Cablink’s certified USB solutions guarantee reliability. Explore our full range cale products at our website and experience the difference expertise makes.